Additive Manufacturing in Launch Vehicles: How 3D Printing is Redefining Rocket Design, Cost, and Sustainability
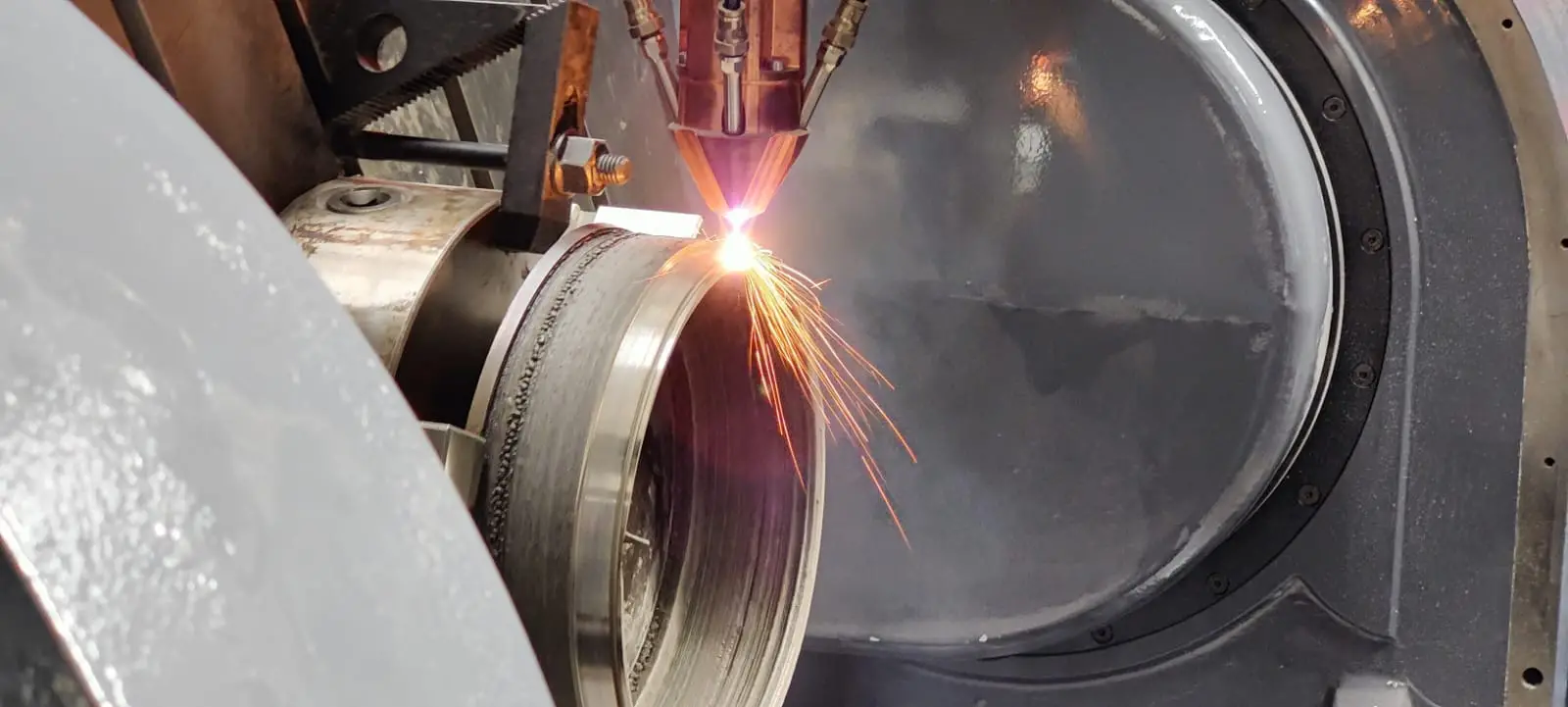
The space industry is undergoing a quiet revolution, driven by additive manufacturing (AM) — a technology reshaping how rockets are designed, built, and launched. From slashing production costs to enabling radical new designs, 3D printing is proving indispensable for companies like Skyrora, which is advancing the UK's sovereign space capabilities with its cutting-edge hybrid 3D printers, Skyprint 1 and Skyprint 2.
Design Innovation: Breaking Free from Traditional Limits
Additive manufacturing empowers engineers to create complex geometries unachievable through conventional methods. For rocket engines, this means integrated cooling channels within combustion chambers and nozzles, optimized fuel injectors, and lightweight structures that reduce launch mass while maintaining strength.
Skyrora’s Skyprint 2 — Europe’s largest hybrid 3D printer — exemplifies this shift. Combining Directed Energy Deposition (DED) additive manufacturing with CNC machining, Skyprint 2 produces rocket engine components up to 2.3 meters tall using Inconel, a superalloy prized for its heat resistance [1]. This hybrid approach reduces process complexity and enables repairs or modifications to existing parts, a game-changer for rapid iteration [2].
Cost and Time Savings: From Months to Weeks
Traditional rocket part manufacturing often involves lengthy lead times and costly tooling. AM disrupts this by enabling direct digital-to-physical production.
-
Skyrora's Skyprint 2 slashes production timelines by 30% compared to conventional methods.
-
Manufacturing Inconel engine components now takes just two weeks, down from 10 weeks.
-
The printer's ability to handle bi-metallic materials opens doors to advanced alloys tailored for reusability and extreme environments.
These efficiencies are critical for scaling small satellite launch services, where speed and affordability are paramount.
Sustainability: Reducing Waste and Enabling Circular Practices
AM’s material efficiency aligns with the space industry’s growing emphasis on sustainability.
Skyprint 2 uses a “near-net-shape” process, minimizing material usage. Any residual material that would be otherwise lost due to blowout is instead collected and recycled, enabling greater material efficiency [1].
This approach supports Skyrora’s broader sustainability goals, including its Ecosene fuel derived from unrecyclable plastics.
By consolidating parts and streamlining supply chains, AM also reduces the carbon footprint of rocket production — a key advantage as regulators and customers demand greener space initiatives.
Skyrora's Leadership in Hybrid Manufacturing
Skyrora’s Skyprint 1 and Skyprint 2 position the UK as a leader in sovereign launch technology.
Skyprint 2 is not only the largest hybrid 3D printer in the UK but also the first to integrate additive and subtractive processes on a single platform [4].
This allows for rapid prototyping, repairs, and large-scale production of critical engine components.
Volodymyr Levykin, Skyrora’s CEO, emphasizes that this technology is central to the company’s mission: “Skyprint 2 reinforces our ambitions to not only be the first company to launch from UK soil, but also to do so in the most sustainable way possible” [1].
The Future: AI, In-Space Manufacturing, and Beyond
The next frontier for AM in launch vehicle manufacturing includes:
– AI-driven design optimization for thermal and structural performance.
– In-space manufacturing of large structures using 3D printers.
– New material science breakthroughs, such as high-entropy alloys for deep-space missions.
Conclusion
From Skyrora’s hybrid printers to full-scale rocket production, additive manufacturing is redefining rocket manufacturing. By merging design freedom, cost efficiency, and sustainability, 3D printing ensures the UK remains at the forefront of the global space race — one layer at a time.
Stay tuned as Skyrora continues to innovate, proving that the future of space exploration is not just written in the stars, but printed on Earth.