Rocket Engine Testing: What, How and Why?
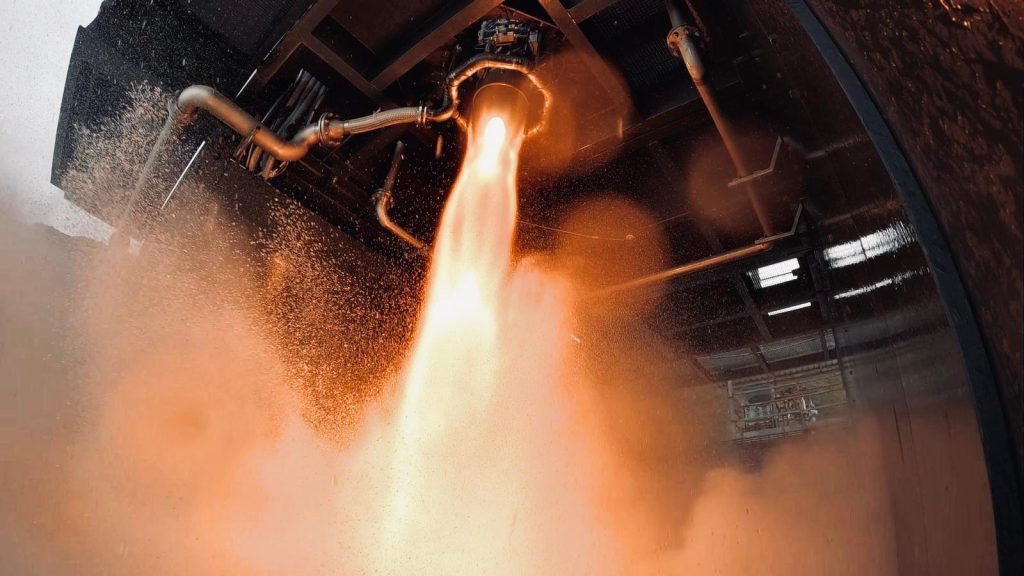
Engine testing is critical for the success of any launch mission. Testing methods have evolved over time, allowing engineers to simulate challenging launch conditions and identify potential issues. Through testing, engineers can improve the reliability and performance of rocket engines, ultimately facilitating successful and efficient space exploration. Skyrora makes use of our state-of-the-art testing facility to conduct such tests as we continue our journey to orbit.
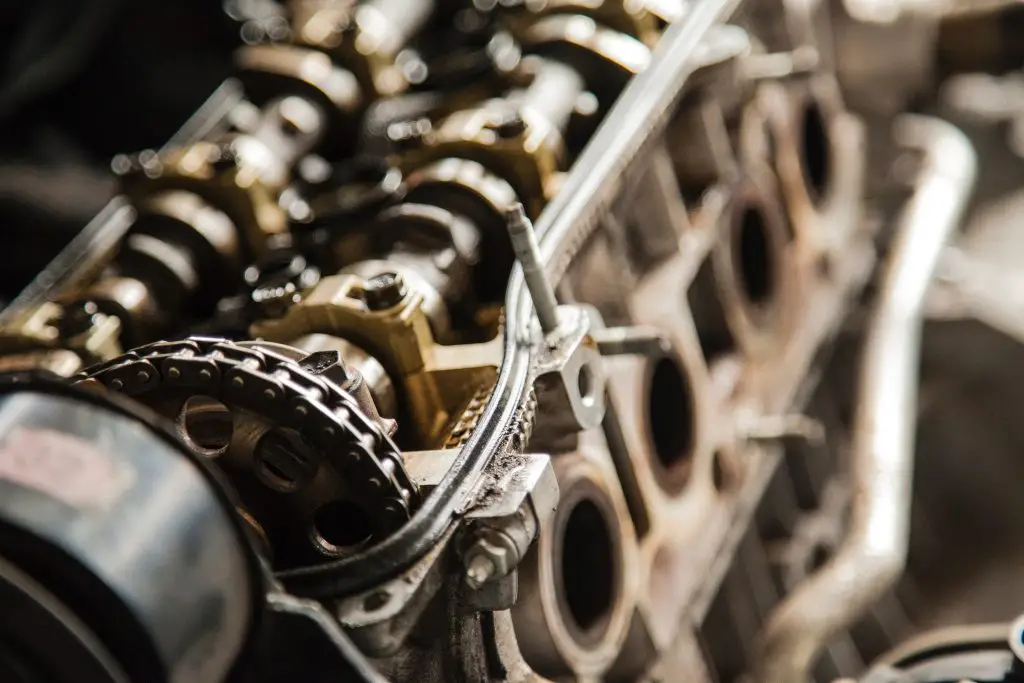
What is Engine Testing?
Engine testing is the process used to assess and evaluate an engine’s performance, efficiency, and durability. It is a critical part of the engine development process in any vehicle, but it is particularly important in the field of aerospace engineering. Engine testing ensures that engines function as they should, that they are safe, and that they meet performance requirements. It’s during the testing phase that any flaws or potential improvements are identified.
Rocket Engine Testing: A Brief History
Rocket engine testing has been a critical component of the development of space technology for over a century. As space programmes have evolved across the world, the importance of testing rocket engines has grown in parallel. The 20th century saw the first explorations into rocketry. Konstantin Tsiolkovsky was among the pioneers who first proposed the idea of using rockets for space exploration. However, it was Robert H. Goddard, an American physicist, who successfully launched the world's first liquid-fuelled rocket in 1926, powered by liquid oxygen and gasoline. This rocket, which was relatively simple and small by modern standards, reached a height of 41 feet.
Goddard’s designs also introduced important features still in use today, such as a combustion chamber and a nozzle for directing the flow of exhaust gases. Many of the patents Goddard received for innovation over the course of his career are still foundational in the field of rocket propulsion.
Perhaps the most major milestone in rocket engine test history was the development and execution of the United States’ Apollo program, responsible for the first moon landing in 1969. The Saturn V rocket carried the Apollo spacecraft into orbit using five powerful F-1 rocket engines. The F-1 remains the most powerful single-chamber liquid-fuelled rocket engine ever developed, with each engine producing 1.5 million pounds of thrust. The rigorous testing of these engines was a fundamental factor which contributed to the success of the program, and to this day they remain the most powerful rocket engines ever built.
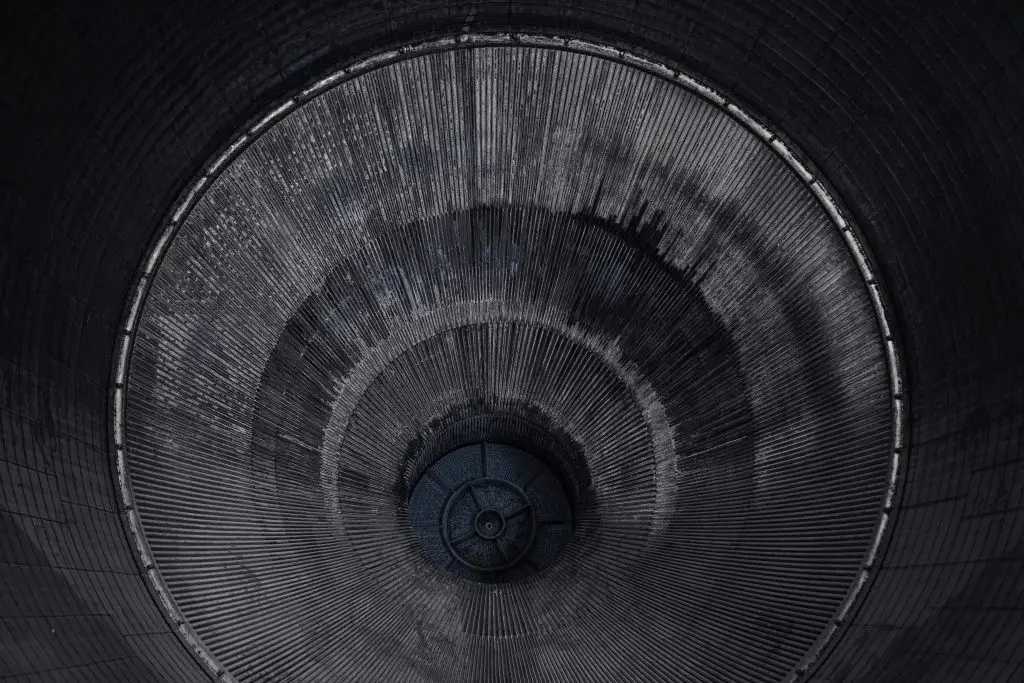
Why Test Before Launch?
The primary reason for rocket engine testing is to ensure an engine’s reliability and performance. Rocket engines are subjected to extreme conditions during launch, such as high temperatures, pressures and vibrations. Any failure or malfunction of the engine during launch can have catastrophic consequences. Therefore, it is critical that the engine is tested under similar conditions to identify any potential issues and address them before launch.
Rocket engine testing involves several stages, including ground tests and flight tests. Ground tests are conducted to verify the engine’s performance under various operating conditions and to ensure its structural integrity.
Achieving this balance is critical in ensuring the spacecraft’s success as well as minimising launch costs. Testing allows for the fine-tuning of an engine’s performance and the identification of any inefficiencies that need to be addressed.
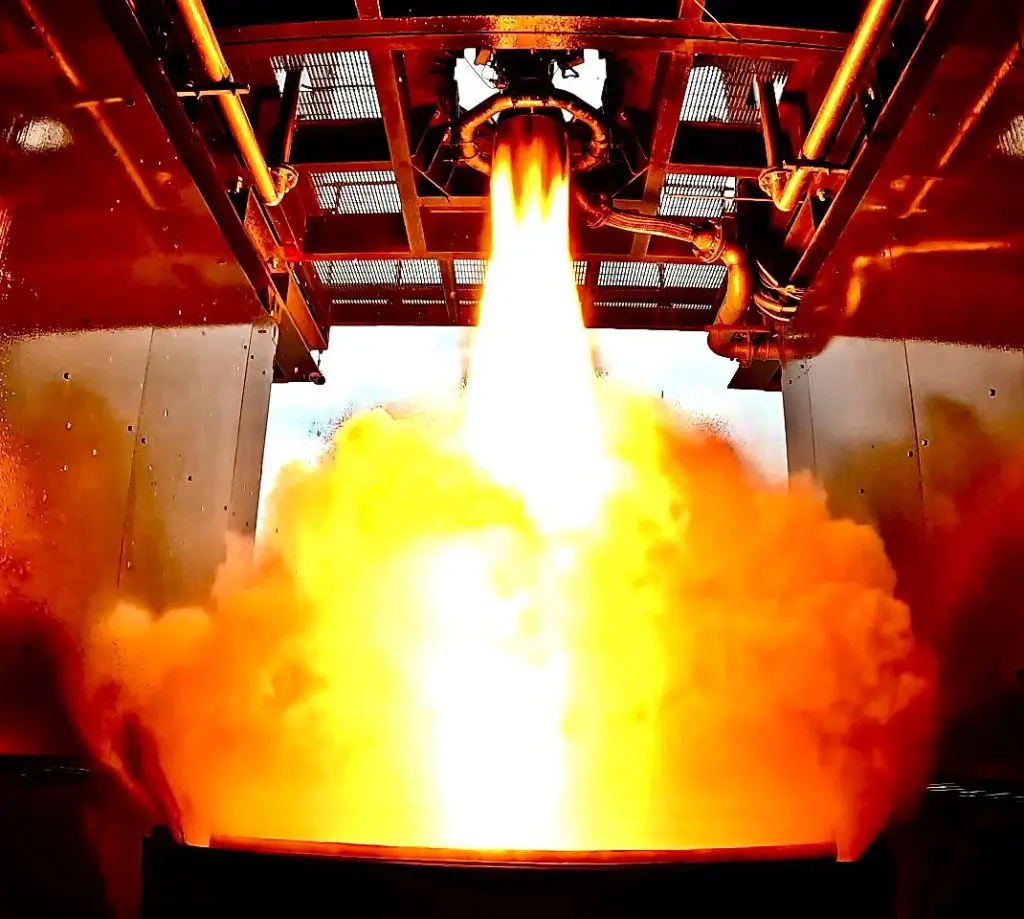
Types of Rocket Engine Testing
Static Fire Testing
This is the most common type of rocket engine testing. In static fire testing, the rocket engine is mounted on a test stand and fired while it is firmly secured to the ground. The purpose of this test is to ensure that the engine can produce the required thrust and operate correctly. This test also allows engineers to monitor the engine’s performance, such as specific impulse, thrust level and propellant mixture ratio.
Altitude Testing
An altitude test involves firing the rocket engine in a vacuum chamber to simulate the conditions of space. Altitude testing is important for engines that are intended for use in upper stages of rockets, where the air pressure is low. Despite this test being the only option to measure close to zero vacuum thrust correctly, often it is not conducted due to the complexity of the required equipment.
Throttle Testing
A throttle test is a type of static fire testing that involves varying the engine’s thrust output while it is firing. This test is essential for engines that need to adjust their thrust levels during flight, for instance the main engines aboard the Space Shuttle. A throttle test allows engineers to verify that the engine can adjust its thrust output smoothly and reliably.
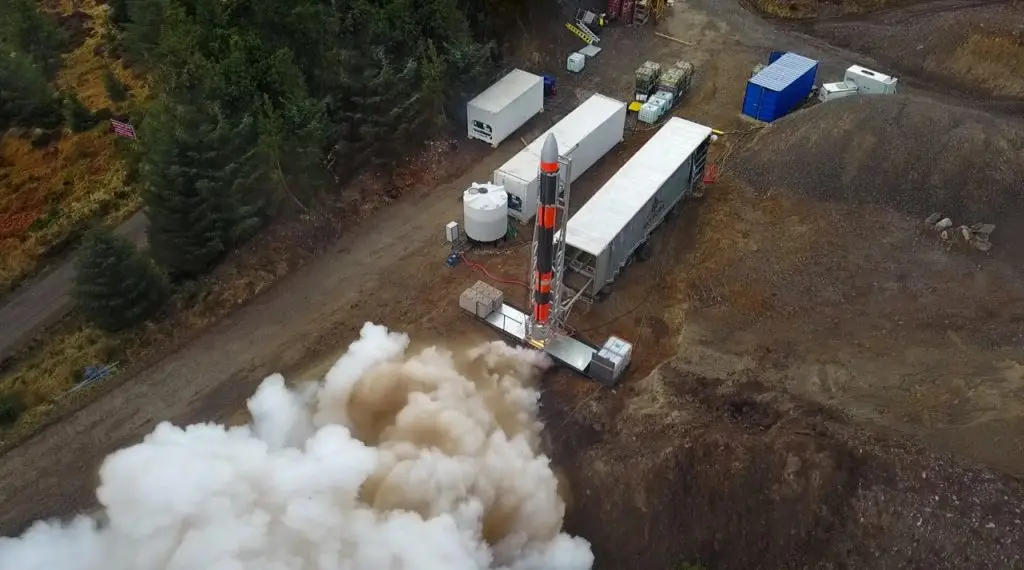
The Evolution of Testing Capability
In the early 20th century, rocket testing was primarily a trial-and-error process. Engineers like Robert H. Goddard would design and build a rocket, then assess the outcome. While they could make educated guesses based on physics and engineering principles, but they didn't have the detailed knowledge or the precise tools to predict exactly what would happen.
With the development of jet engines and the start of the Space Race in the mid-20th century, more sophisticated testing techniques became necessary. Wind tunnels were used to test the aerodynamics of rockets. More advanced computational models were developed, allowing for the simulation of rocket flights before they occurred. Still, the models were relatively basic by today's standards and the computer hardware available was limited in its capabilities.
In the latter part of the 20th century, sensor technology improved, allowing for more detailed data collection during tests. These sensors could measure everything from temperature to pressure to acceleration. This data could then be fed back into computational models to improve their accuracy. Meanwhile, the growth of digital computing power allowed for more complex simulations and models.
In the 21st century, computational power and software sophistication have grown exponentially. Simulations can now model the entire rocket, the environment it is in, and the physics of its operation in extreme detail. This allows many potential problems to be identified and corrected before a physical rocket is ever built.
The advent of 3D printing technology has also had a significant impact on rocket testing. It allows engineers to produce parts quickly and inexpensively for testing, as well as enabling parts which generally require assembly in multiple pieces to be made in just one piece. This is a method Skyrora employs in the in-house development of rocket engines.
SpaceX's development of reusable rockets has necessitated new testing methods as well. Traditional rockets are used once and then discarded, but SpaceX's Falcon and Starship rockets are designed to land back on Earth and be flown again. This means they must be tested not just for launch, but for re-entry and landing as well.
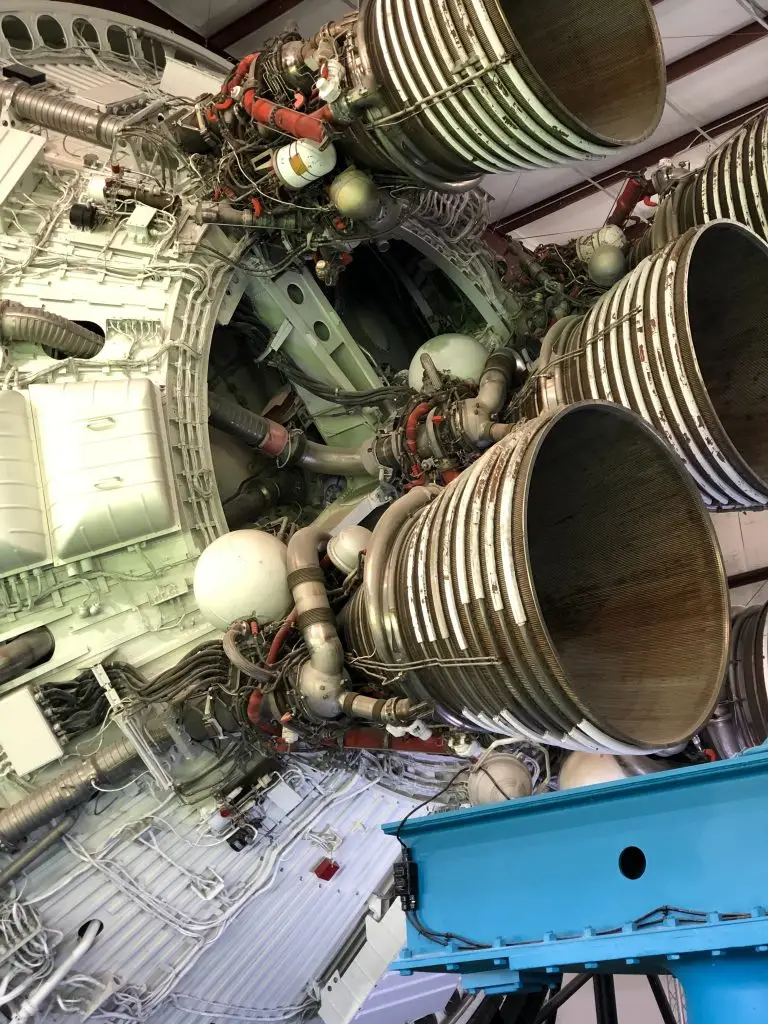
How is Engine Testing Conducted?
After individual components have been tested and validated, they are assembled into a complete rocket engine.
Once assembled, the engine is ready for testing. Most engines undergo a series of cold flow tests and pressure tests, where the fuel and oxidiser are flowed through the engine without being ignited, to verify the flow paths and check for leaks. Following successful cold flow tests, ‘hot fire’ tests are conducted where the engine is ignited, and its performance measured. After individual engine tests, the engines are integrated into the rocket body. This integrated vehicle is then also tested, including static fire tests where the full rocket is held down on the launch pad and the engines are ignited.
Testing is usually performed at specially designed facilities which can safely withstand any nominal and off-nominal situations. These facilities are usually located in remote areas due to the noise and potential safety hazards associated with engine tests.
Engine test facilities are meticulously prepared for rocket testing. The readiness of all infrastructure, including the structure set to hold the engine during testing and mission control areas, must first be confirmed. Mission control and further accommodation for persons on-site ensure individuals remain at a safe distance from live tests.
Once all individuals are at a safe distance, propellant is pumped into the engine. Propellant tanks are monitored during this process to weigh the fuel before firing, allowing researchers to determine how much is burned during the test. To gather further data from the engine tests, numerous sensors feature in and around test equipment, including load cells, thermocouples, and pressure gauges. Engineers are always present in the control room, monitoring data to ensure normal engine performance. In the case that an engine does not perform as planned, the test is aborted by mission control.
Following the test, normally consisting of no more than a few minutes, engine shutdown is completed. The area is rendered safe for inspection, and the site is reset to accommodate future tests.
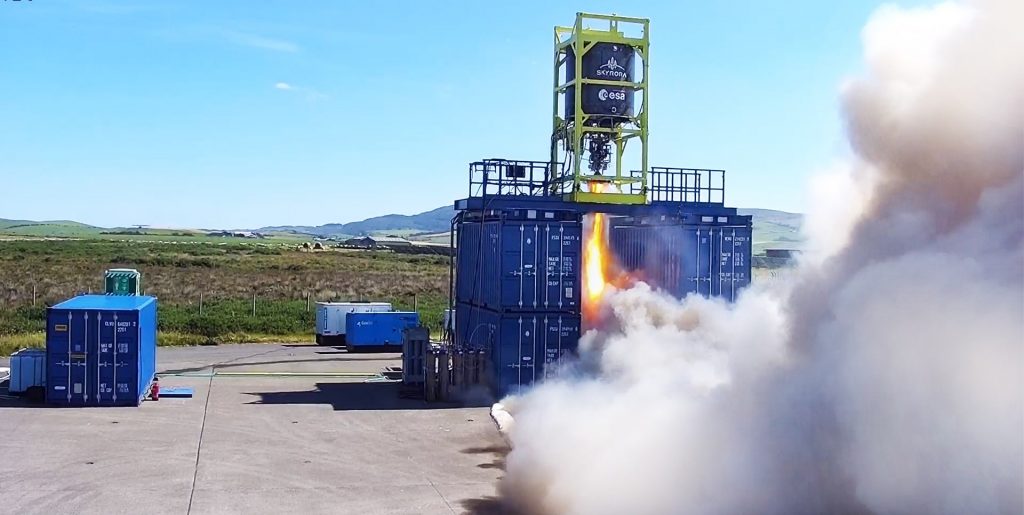
Skyrora’s Engine Testing
Skyrora’s engine testing activity is carried out at our state-of-the-art test site in Gorebridge, Midlothian, the largest of its kind in the UK at more than 120,000 sq ft.
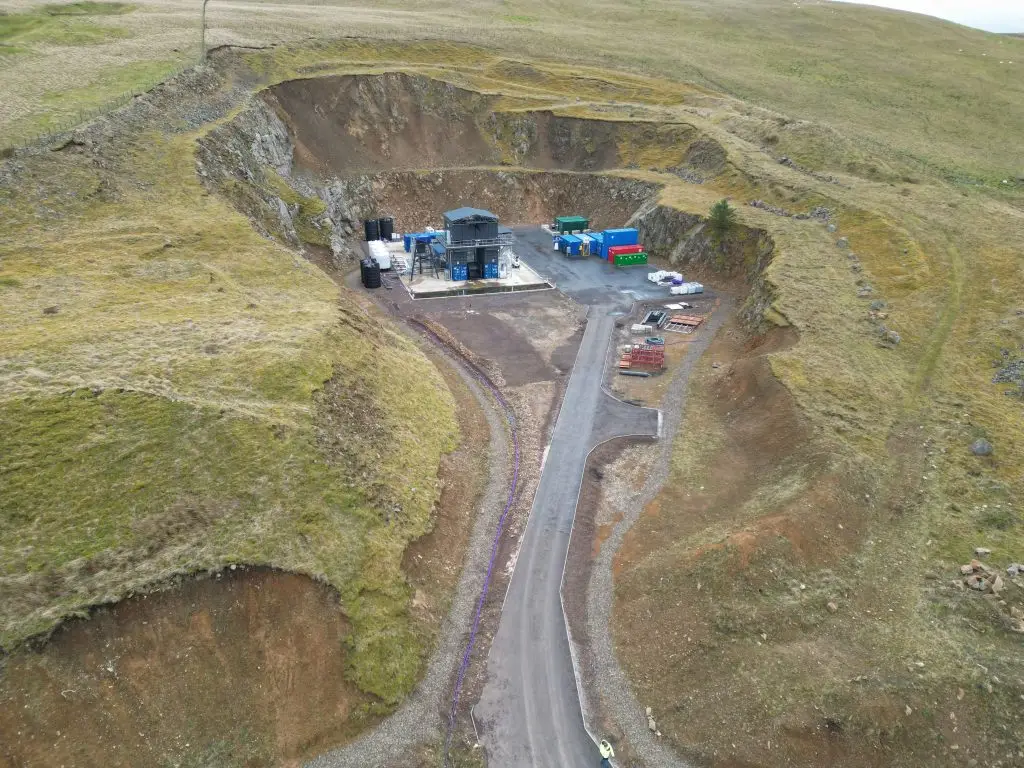
Skyrora’s progress in engine testing began with the first ground test of our LEO engine in 2019, verifying its performance and structural integrity. A longer fire was conducted on the same engine in 2020, again successfully demonstrating its reliability and performance.
More recent engine testing has been conducted on Skyrora’s 70kN rocket engine, set to be the first staged combustion engine on high-test peroxide (HTP) and kerosene when qualified. This fully 3D-printed engine will be used on both the first and second stages of Skyrora’s XL orbital vehicle. Skyrora is set to continue an upward trajectory in engine testing throughout 2023, with a series of static fire tests of our first and second stage 70 kN engines, furthering the technological readiness of Skyrora XL. These tests are being conducted in line with ESA’s Boost! programme, which continues to support us in our journey to orbit.
Perhaps the most significant of Skyrora’s recent engine testing was the hot firing of the full second stage of orbital vehicle Skyrora XL. This 20-second burn saw all systems remain nominal, with the 70kN liquid engine achieving the required thrust. This 2022 test proved the vehicle’s operational capability for its intended payloads and demonstrated that its performance meets all design requirements ahead of orbital launch.
Ultimately, Skyrora’s engine testing program is a testament to the company’s dedication to innovation and excellence in rocketry. Through its testing program, Skyrora is developing reliable and efficient rocket engines that are pushing the company closer to becoming a commercially viable UK-based launch provider.
References
1. Choi, M. (2019). The Ins and Outs of Propulsion Testing. [online] National Technical Systems. Available at: https://nts.com/ntsblog/propulsion-testing/.
2. Glenn Research Center | NASA. (2018). Conducting a Test – Glenn Research Center | NASA. [online] Available at: https://www1.grc.nasa.gov/historic-facilities/rocket-engine-test-facility/conducting-a-test/.
3. Anon, (2021). 95 Years Ago: Goddard’s First Liquid-Fueled Rocket – NASA. [online] Available at: https://www.nasa.gov/history/95-years-ago-goddards-first-liquid-fueled-rocket/#:~:text=Goddard%20began%20experimenting%20with%20liquid.
4. Glenn Research Center | NASA. (2018). Apollo Era Testing | Glenn Research Center | NASA. [online] Available at: https://www1.grc.nasa.gov/historic-facilities/rocket-engine-test-facility/apollo-era-testing/#:~:text=These%20studies%20began%20on%20Nov.
5. Engine Testing Overview. (n.d.). Available at: https://users.sussex.ac.uk/~tafb8/eti/eti_03_EngineTestingOverview.pdf.